Automatic Foil Stamping and Die Cutting Machine
This product has been discontinued and removed from our shelves.
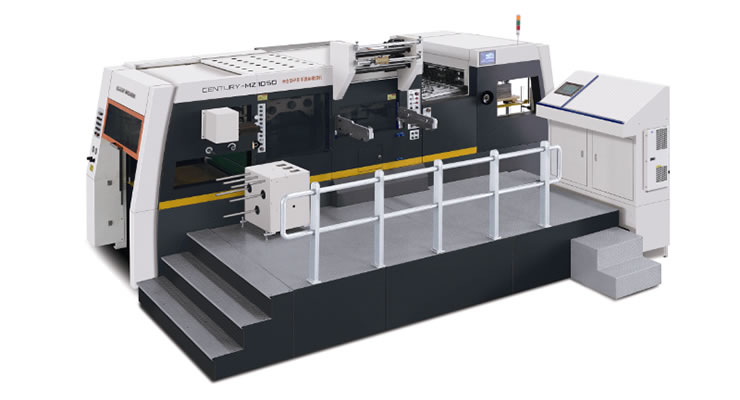
The MZ 1050J automatic foil stamping and die cutting machine commonly used for packaging and decoration for paper foil stamping and die cutting.
This foil stamping machine uses a Japanese servo driving and control system, which increases the memory of the machine.
Four servo motors separately control the die cutting machine's foil rolls for a high precision on the foil stamping.
A 12 temperature zone control system is used for high quality foil stamping.
Model | MZ 1050J |
Max. paper size | 1050*750mm |
Min. paper size | 400*360mm |
Max. die cutting size | 1040*730mm |
Max. stamping size | Transversal: 1030*600mm; Longitudinal: 1040*730mm |
Heating panel power | 22.3 KW |
Stock range | Cardboard 90-2000g; Corrugated board≤4mm, |
Max. temperature of stamping panel | 199°C |
Max. pressure | 300 Tons |
Max. cutting speed | 7,500s/h |
Max. stamping speed | 6,000s/h |
Heating zone | 12 |
Foil feeding shafts | Longitudinal 2; transversal 3 |
Max. foil roll | Transversal Ф200mm; longitudinal Ф250mm |
Foil stamping accuracy | ±0.15 |
Power consumption | Die-cutting is 29 KW, Foil stamping is 67.6 KW |
Machine dimension (L*W*H) | 6000*4400*2700mm |
Machine weight | 18 Tons |
Feeding Section
The foil stamping machine uses a customized feeder system
A flute to double wall corrugated board.
Four pick up and four forward suction heads carry out angle adjustment.
It is applicable to cardboard 100-2000gsm and E, F, C, B flutes.
The feeder is an automatic, non-stop feeder and pre-feeder, allowing for a high efficiencyTransversal Foil Stamping
Two groups of electrochemical foil rollers are transversely used with a separate control by 2 sets of AC servo motors. It can achieve jump and stepping functions separately in order to be retractable synch/consistent in the production of the aluminum foil in order to ensure a high stamping accuracy.
Longitudinal Foil Stamping
3 electrochemical aluminum foil step rollers are used in the longitudinal hot stamping section, which is controlled by 3 sets of AC servo motors.
Die Cutting Section
The die cutting section has a pneumatic button die chase locking mechanism to ensure a safe and easy change of the die cutter plate.
This section uses internationally known brands in the bearings and electrical components for precise control of the die cutting process.Delivery Section
The delivery section utilizes a non-stop delivery system.
Side and front joggers ensure neat stacking.
Two delivery options are available: pallet or trailer.
A photoelectric safety device is sued for safe entrance and operation.Human Machine Interface
A colored touch screen is used to monitor machine status and diagnose problems.
Electrical Control Section
Siemens latest PLC technology is used to ensure a safe and trouble free operation.
The electrical control section uses components from internationally known brands for a better performance as well as fast, local after sales service and maintenance.
Equipped with a number of safety devices, the machine will alarm and stop automatically when faults occur. This ensures the safety of both the operator and machine.